Self Build & Renovation: Live! by NSBRC - Episode 6 - Battle of the Building Systems
Download MP3Good morning.
Welcome to Self-Build and Renovation Live.
Apologies we're a little bit late.
It does prove that we are
definitely live because
we've got an event going on
that either costed our
guests for this panel fight,
I'm going to call it today.
I feel like I should be in a
ref's outfit to be honest with you,
but it'll be great fun.
We're going to enjoy this one.
We've got them and we're ready to go.
My name is Chris Dawes from Visual PR,
but let's find out who the
most important people are.
So one at a time, introduce who you are,
where you're from, and of course,
what you're representing
from the building systems fight.
Yeah, I'm Rob Clark from Honka UK,
and we import wooden homes
from Finland that are cross-laminated,
very healthy to build.
But that's your speciality.
That's our speciality.
I like it.
That's why we started
talking about ice hockey earlier as well.
Exactly.
Yeah, yeah, yeah.
I've got it.
And next,
Steve Callow from the Mineral
Products Association, MPA Masonry.
We represent masonry
suppliers to the Southfield market.
And obviously we speak on
behalf of what people think
of as traditional brick and
block masonry build systems.
fantastic thank you sir good
morning yeah I'm max ellis
I'm from fleming homes
we're a timber frame
manufacturer so I'm
representing timber frame
fabulous which I think
we've kind of got some
behind us to some extent
there and you bought
examples next yeah yeah I'm
richard leonard I'm from
beaker war form beaker war
form is an insulated
concrete formwork system so
large polystyrene blocks
which you fill with concrete
which you actually stole the
intended filming space.
We did, yes, I'm very sorry about that.
By building something just yesterday,
a whole thing,
which kind of proves its point, I think,
to some extent, doesn't it?
Yeah, absolutely, yeah.
Next.
Hi all,
I'm Phil Bagnell from Evolution
Home and Leisure.
We are a steel frame panel manufacturer.
So we're a complete manufacturer,
and so I'm representing
steel framed panels, insulator panels.
So as you can see,
we've got the full spectrum covered here,
which is why it is roll our sleeves up.
I apologise in advance, by the way,
if there's at times when we
might be a little bit
difficult to hear or you
hear a hum in the background,
as you all know,
it is a little bit bitter
out there today.
And so we've got the heating
going absolutely mental today.
So, yes, bear with us on that one.
Thanks for a couple of
comments coming in as well.
Eleanor Van Ploew, good morning to you.
And Sarah Troughton, just quickly.
You can put your comments in
and we're able to put them up on screen.
Sarah Troughton, is there a problem?
Now you know the answer to that one.
There was just a slight delay.
So thanks for bearing with us.
Much appreciated.
um right so I'm going to
come the opposite direction
this time and make sure we
can hear you with this one
because this is the
critical one now is what
are the main advantages of
using your building system
all right now is your
chance to put your warfare
down uh and in what
scenario uh does your
building system particularly shine
Okay, like I said,
we are a steel-framed manufacturer,
and so we design, manufacture,
we do everything in-house.
There isn't anything we put
out to any other company.
So as a self-builder,
you can come and sit down with us,
go through a particular design,
and we can panellise that for you,
help you cost it.
You can then take that
design to an architect or
come to us with an architect's design,
and we can go through everything.
can show you our complete
process within the factory
so order process
manufacturing process
installation process once
we've gone through all that
you can even actually come
and get involved with us
and work with us creating
and producing your own
panels and also on site as
part of the installation
team as well so with us you
can do as much or as little
as possible you can either do
virtually everything and we
only put a two-man team on
site helping you actually
do the installation and
also in the factory like I
say you can come and get
involved with the actual
manufacturing and putting
together of the panel so
you get complete
understanding of everything
So that's one of our,
we'd like to think as a USP,
something that we're able to do.
And like I said, as the manufacturer,
that gives you the
opportunity to get involved
and look at everything.
Because presumably it is, yeah,
with the steel framework,
it is built bespoke to what you're
design needs to be we
because we're a panelized
system we we have various
standard panels so once we
once we've sort of put them
panels together and and
then to create to go into small gaps or
to adjust our panel size to
whatever your architect has
designed for you or you're looking at,
then we're completely bespoke.
We can build any size panel,
width or length up to ten foot tall.
If we need to go more than ten foot tall,
then we just put a strap in
and go another foot high.
And what's a key benefit or
what would make someone
feel that steel framework
was the right way to go for their build?
We're actually the only
company that's overcome
cold bridging within a steel frame.
So we don't have a cavity.
We've actually painted or
painted pending on the fact
that we've overcome cold bridging.
So we can create a single
panel system with new
values on our single panel
of about point one three
before we add anything else
to it internally or externally.
and we get excellent air
tightness of point two six
or two point six.
So two point six on air tightness,
just a standard.
So just as a standard
offering into the market,
that's what we're coming at
before we start getting
other experts involved in
getting to pacify standard
and things like that.
Okay.
Do you find that people
already have decided that's
the route they're going,
or would they still be
potentially unsure?
No, I think people want to go to passive,
but I can't get a
definitive answer as to
what the extra cost is
going to certified passive
against getting to passive
but not being certified.
I think people want to build
to that standard,
but I think they're not
sure where the additional
cost is or how big that cost is yet.
Well,
I know that episode seven in about
two weeks time, twenty first,
I think it is episode seven.
We're doing this.
Got the thumbs up.
I was right.
I remember occasionally
we're doing a bit on
Passive House as well
because it's quite an
intriguing area in itself, isn't it?
Hence,
we've already done one episode on
Passive House that's worth
looking back on the YouTube
channel for the NSBRC's YouTube channel.
Thank you very much for that, Phil.
Richard, I mean,
I feel like I should almost
say that yours is possibly
the one that people don't
necessarily realise about
more than any of the others, because
when you look at it and you've got it here,
polystyrene.
But that's not the whole story, is it?
No.
So with insulated concrete
formwork like Warthorne,
I would say the primary
advantage to it is its energy efficiency.
And that's in that it
delivers in three different ways here.
So we've got a lot of
insulation to give us a very low U value.
So this particular wall
block I've got here gives
the U value of point one four,
which is suitable for passive house.
and we have to have one
that's slightly wider still
but will give us a new
value of point one one so
we've got the insulation
aspect to uh low energy or
zero energy construction
the um post siren because
it has to completely
contain the concrete during
the construction process
because we're filling this
core with our concrete to
give us our structural
element it means the
continuous form work being
insulation eliminates
co-bridging because if the
concrete if the
insulation wasn't continuous
the concrete would escape
so it was a definite proof
of point there but we've
got our continuous layer of
insulation in the build and
because as the concrete
goes in it naturally seals
up to the previous pour and
we have relatively few
concrete pours over the
duration of the build maybe
three or four if we're
using a concrete pump it
means we naturally achieve
a very airtight structure
as well so it's doing the
three key principles of
passive house design just
within this one relatively simple
I always make an apology and
I do to all of you here.
I'm from outside of this industry.
I'm just doing the host role
here and I love doing this
because I'm learning every episode.
It's absolutely brilliant.
Am I right, and I apologize if I'm not,
that that is an area that
maybe people don't
automatically think of and
you've had to educate people?
on this or on my role?
To a certain degree, yeah.
We do produce different
levels of insulation within our system.
So we can start at building
regulations level and
progressively go down to
full passive house performance.
And so it really just
depends what position
people are in their project,
what direction they're
coming from as to which of
our systems they might choose.
And very often,
they may come across
insulated concrete formwork
for a different reason for
example if you wanted to
build a basement which you
can also use it for and
then that then leads on to
as they discover the system
what it's capable of then
perhaps um that's how they
then realize that there is
actually that potential to
to go full passive or close to passive
yes absolutely and I'm going
to ask a really stupid
question I know the answer
but I want to hear it from
you obviously I mean we've
got an example down behind
us that you guys bought a
built literally yesterday
yeah but it's not that
we're suddenly going that's
what your house now looks
like there it is covered
around the outside yes with
what absolutely on the
outside you've got a full
range of choices um I would
say the most popular cool
is probably render still
okay on the render systems
which can software straight
to the outside panel
uh but equally we see brick
slips brick skins stone
skins um even sympathetic
that's that seems to be
growing popularity just at
the moment along the inside
it can be wet plaster or
plasterboard straight to
apply styling okay that
makes sense but give me for
a second max because I'm
just going to briefly jump
out jump over you um
because steve I'm almost
thinking obviously from the
mpa masonry side there's a
crossover here for sure
they're some of our members
as well and you know i
We have members that produce that product.
We have members that produce
it in woodcrete as well
within it as the same form.
Woodcrete.
similar shape exactly what
you're looking at there but
a calcified form of timber
that has incredible kind of
long durability as well
similar there's many
examples in the the um in
the center that can show
you them but very similar
to that and again the core
of it is like a concrete
structural framework it's
durable it's going to last
for a long time we're a big
supporter of it
and and if you don't mind
I'll come back to you max
is that it makes sense for
you to now also answer the
question fully about you
know um what are the main
advantages from your
perspective of your
speciality obviously the
masonry side um and and
where would someone be
using that so we do have a
representation for the icf
the the concrete frame um
manufacturers but we
primarily represent the brick and block
manufacturers within the uk
so mostly on the block side
of things um something that
everybody's seen you know
this has been the de facto
sort of build method in the
uk for north of sort of
seventy five years or so um
you know cavity that
everybody recognizes we
have brick outside um
insulation cavity and then
we have a block in a wall um
You know, the reason we promote it,
the reason we're really
very passionate about it is
it's not just this being
the default build method.
It's got a lot of material
properties that we really believe in.
You know, it's durable.
It lasts a long time.
You know, I've been a self builder.
I've done self builds in the
past and I picked that material choice.
because I like the
properties of what that
brings we call them
heavyweight builds you know
they've got some thermal
property advantages you
know a lot of people have
questions one of the
biggest ones we get asked
about is um energy
efficiency and and you know
how other material sort of
choices can be perceived to
be a lot more energy
efficient the first build
that meets the future home
standards coming in that
was done in the uk we need
to exceed it project at was
done and they picked
brick and block for a reason
to prove that that build
method could hit that target.
So, you know,
there's answers to all the
same with the other build method.
It's always a question of like,
ask the question and listen
to the people that
represent that sector
giving you the answer that
You need to know and
understand whether that
fits with what you need.
We have the answer.
You know, we like the material properties,
the thermal mass,
all that stuff that we get
with heavyweight build.
That's why we like that material.
But there's also other bits
in the background where
people will be asking you
questions and we have answers to those.
That's our kind of role in
this is to give you that
best practice kind of
guidance and answer the
questions that we know
we're going to be coming about.
which I would imagine is an
awful lot and I do for sure
hasten to add here is that
don't expect today's
episode to give you all of
those answers from every
single one of these things
it just isn't possible
there's too much to talk
about too many nuances I
would imagine for the
situations but if anything
it's to start making you
aware that there are conversations
to be had and I think that's
the key one and we've got
and I'm going to put it up
again uh on here is that
the link that shows we've
got the say that my mouse
isn't working um click not
working but uh it's going
to put the web link up for
the for the show um oh
that's because I've frozen
that's why it's not showing
my screen frozen but there we go um
january thirty first
february first and second
we've got a three-day show
here and you can get here
and you can speak to all of
these experts you can go
and look at all of the
stands and and uh and and
find out more and that's
the critical thing isn't it
max back to you now I do
start feeling that we are
getting that ramping that
tension up now between the
different methods
And I'm okay with that, if I'm honest.
I'm okay with it.
But obviously,
we're now going in a
different direction again.
So we've gone steel,
we've gone the polystyrene with concrete,
we've gone the concrete and brickwork.
We're now going wooden.
Yeah, so timber frame.
And, you know,
I'll ease that tension down a little bit,
perhaps by saying...
There are so many options
out there nowadays for the
sort of builder and the self builder.
And when I give these sort of talks,
I always say, you know,
we can all pretty much get
from A to Z and all the
different systems in this all today,
you know,
we can all get to where the
customer usually wants to be,
but it's their job.
to find out what system's
best for them yeah um but
anyway I'm here to promote
timber frame so uh I like
your your passive way yeah
yeah yeah yeah yeah but
yeah timber frame benefits
I suppose the two most
commonly known benefits
with timber frame are the
speed of construction that
you get with it
You know,
we can usually get a customer's
house to wind and water tight stage,
which means the structure erected,
windows and doors installed,
roof bordered and membrane.
So, you know,
you've got that wind and
weather tight shell.
You know, on an average size house,
we're usually on site about
two to three weeks to get
them to that stage.
There's a big benefit for
them to say that that initial big change
part of the construction
process is fairly quick yes
um the other sort of most
commonly known benefit I
suppose is the thermal
efficiency that you get so
with timber frame usually
the the primary insulation
core is housed within the
the timber frame panel yes
so and that's usually
factory fitted so um with
this one you can see behind
me uh we use an open panel timber frame
You've got the main body of
insulation that's housed
within the timber frame panels.
And as you can see there,
we've included another additional layer,
which takes that wall from
probably just about meeting
building regs or a bit
slightly better down to a
low energy level.
so with that type of system
the customer can choose how
well their wall is going to
perform so that particular
example is showing a
hundred and forty mil
timber frame stud with
insulation housed within it
an additional fifty mil
gets you down to about
point one one new value
which is a sort of you know
very good sort of performing wall so
they're the two main
benefits speed of
construction on site
thermal efficiency but
there are lots of others
you know um flexibility um
ease for the client so on
and so forth sustainability
um but also what a lot of
companies are finding out
specifically in this market
that south builders need a
bit of help elsewhere so
it's not just about the
product perhaps it's also
what that company is going
to offer in terms of the
bolt-on services that they
offer for example remember
to do your planning
application for you we're
building race drawings or
put your foundations in so
um yeah um it's um lots of
different uh bolt-on
products that might sway it
for the customer not just
the actual build method okay
you able to get as far as
passive house as well yeah
yeah we can do yeah our
system isn't certified um
primarily we don't do that
the slab as part of our
remit and you'd normally
but yeah um if a customer
comes to us and wants
passive we can go and work
yeah as somebody alluded to
a lot of customers when
they start on the journey
got that goal of getting to
passive house levels,
which is a great goal.
It's the Rolls Royce of build performance.
A lot of our customers will
end up just getting a
really good thermal envelope,
fabric first thoughts,
getting a really airtight
and thermally efficient structure,
but they may not quite go
to the fortification stage.
Okay.
Yeah, that makes sense.
And it's aspirational, I guess, isn't it?
I've got to say I keep
chuckling inside I feel
like the big bad wolf and
you know the different
types of housing that we're
talking about here it's
just quite amusing um last
but by absolutely no means
least we've got robert clark from honka
kind of across over here I'm
assuming because yours is
is timber but very much
scandinavian folks
scandinavian yeah well
nordic nordic yeah that's
the one yeah yeah it is I
mean we're using massive
wood uh basically so
instead of the timber frame
uh system that max has got
there you know our walls
are solid wood wow yeah um that come in
what you would traditionally
have called logs,
but it's cross laminated
timber that we're using.
And the main reason that
people choose our product, A,
we're a company that's been
trading since nineteen fifty eight,
built more than ninety
thousand houses around the world.
So there's a lot of experience there.
We know what we're doing and
it's probably one of the
most sustainable building
systems there is.
I mean,
the more wood that you use in a building,
the more sustainable it will be,
provided the wood's coming
from sustainable sources.
We're binding lots of carbon
into the houses,
so a traditional sort of
three-bedroom house will
bind about ninety tonnes of carbon,
so that's quite significant.
That's the equivalent to
driving a family car about
fourteen times around the world,
so it's quite a lot of carbon.
And that's bound into the
building for life.
And the other benefit of
this system is it's
incredibly healthy to live in.
So we don't get any mold spores.
There's no dust in the air.
There's no bacteria.
The walls are actually
naturally antibacterial.
And we can also prove that
it reduces your heart rate.
So you'll have about ten
percent less heartbeats per day.
It's about eight and a half
thousand less heartbeats
per day if you live in one
of these houses.
So you feel more relaxed.
You sleep better.
It can reduce your blood pressure.
So a lot of health benefits
that have been in this type
of house as well.
Okay.
I do love that.
That's solid, isn't it?
Well, it is a very tactile product,
you know, and the thing with wood,
and again,
one of the benefits of this
system is the wood is
naturally controlling the
environment inside the house.
Right.
So particularly this time of
the year and in the spring
when the sun's coming in
through the doors and windows,
that sun energy still has,
or the heat still has energy.
That gets absorbed into the wood.
So if you feel that,
it's actually quite warm
because it's trying to
equalize the air temperature.
Yeah.
So what happens is overnight,
particularly at the moment
when it's so cold,
the air temperature drops
and the heat that's in the
wood gets released back into the house.
So it helps to reduce your energy costs.
And like the other guys were saying,
you know,
we get asked about passive house a lot.
When you actually drill down
and you question a client
about why they want passive house,
you realise that a lot of them,
I would say at least ninety percent,
don't actually want passive house.
They just want a house
that's energy efficient.
Yeah, exactly.
So, you know, when we say to them, well,
we can build you a house
that's going to cost you
less than ten pounds a month in energy.
They say, well,
that's that's exactly what
we're looking for.
You know,
passive house is less important
than that.
I guess we've got the
ability to get to Passive
House potentially with all
of these different ways.
I would imagine all the systems, yeah.
And like I say, it's aspirational,
which I think even if
someone can't get there,
if you didn't have that
aspirational level,
we probably wouldn't have
people getting up this high, would we?
No.
It's like they say, aim for the sky,
that's as far as you'll get.
Aim for the stars and you
could get through the... Absolutely.
etc etc that kind of stuff
yeah okay um right now that
I've stoked this one up
from you all then uh I like
that one how does um
affordability compare
across these different
building systems um and I
don't know whether we're
able to go into things like
cost per square meter
potential impact of rising
material costs and I'm
gonna go this direction this time
Well, are you ready to go?
Yeah, I'm happy to go.
Go for it then, Phil.
Give us an idea.
So how does the affordability side?
Okay.
where where we like to to
gain is like on timber
frame we're very fast so
we're fast on site we'd be
similar perhaps a week two
weeks to build a hundred
hundred and twenty square
meter house um
superstructure roof on
windows and doors fitted um
so we can save you can save
money in that area and you
can be into it a lot faster
especially if you're going
to perhaps hire a mobile
home which a lot of people
do don't they while they're going to be
building their own house.
Material costings, we've been pretty flat.
We've got three major materials,
which is our insulation,
our steel and our cladding.
And one seems to be up and
the others will come down.
And so
I haven't priced anything
yet and done a job where
we've got to go in and say, look,
we've got a price increase
actually even up to a year.
Really?
Yeah.
Even up to a year.
I haven't had to do that.
And also where the biggest
thing that probably most of us was HS too,
because so many materials,
the price just went up ridiculous.
So, but that happened for everyone.
So I don't mind that it affects everybody.
That's that's okay.
Square meter price.
Varying on the size and the complexity,
fully installed and delivered,
the structure, so the superstructure,
we can be anything from
four hundred and fifty
pound a square meter to five to five,
depending on the complexity
of the building and how big.
um but yeah that would be
and then basically people
are then looking at all the
bolt-ons and the add-ons
but that's for completely
sealed building once you
put the windows and doors
in completely sealed
airtight mortar type
structure with um first
floor and the loft and the
roof everything water proof
base wow so that's what
we're and and like timber
frame we're there in less
than two weeks okay on site
and um there's no power tools
so we're everything is done
with a an allen key so our
walls are fitted together
and held together yeah with
an allen key so there's
you're not even charging
batteries and things like
that so yeah it's yeah so
best out I mean that gives
us good idea I've been
given a ten minute warning
so I'm going to make sure
that we get through
everybody so everybody gets
to say no no no my fault uh
richard the same question
to you sort of like what
are we looking at cost wise
so cost wise with icf
Our feedback we get is that
it's comparable to standard construction,
masonry construction.
The cost profile is probably
the biggest difference.
The actual materials are the
more expensive part of the build,
but the savings come in the
time and the labour.
So because it's so much
quicker and we're not
reliant on bricklayer levels of skill,
it's a semi-skilled construction.
construction system in that respect.
That's where the big cost savings come.
And depending on where you are,
building in the country,
that can actually come quite significant.
And so those two things
together tend to bring us
back out to approximately
about the same sort of cost
as the mainstream construction.
Now,
some of the variation can come in with
the external finish,
because not all external
finishes cost the same.
So render and sympathising
might be the lower cost end.
that comparison.
A full brick skin or stone
skin on the outside of the
gonadosis system might take
it slightly higher.
So again,
it all just depends on what's
involved in the... It's not
easy for you guys at all, is it?
I mean, it really is a lot more to it.
I'm going to very quickly
jump because we've also got...
uh sarah torton apologies if
I pronounce that wrong
sarah uh richard does the
polystyrene of icf get
nibbled by mice uh we're
keen to build with icf but
our current house next to
the site has mice in winter
would woodcrete be a sell
for option for us
Well,
the polystyrene itself has no
nutritious content,
so there's nothing there
that will actually nourish the mice.
So there's no reason for
them to go for it.
But the kind of like the
bullet proof is about is
the external cladding,
because once this is clad on the outside,
effectively it's sealed.
So there should be no access
whatsoever to that.
Just checking what we got another one.
I'm going to put this out there.
Hannah says,
what is the only sustainable
building material, discuss,
unless you use mostly wood
in the superstructure like Honka,
how can the other systems
be ecological and have
sustainable benefits?
Right, there you go.
There's a grenade.
I'm happy to answer that one.
Mineral products are a local material.
People don't realize that
they don't travel, you know,
all block manufacturing.
What was going to say in
answer to the question about cost?
You know,
we don't talk about what specific
costs are because we
represent all the different
manufacturers and be
different in regional areas.
but um you know mineral
products are on this
massive journey to
decarbonize since the
nineties we take up fifty
percent of the embodied
carbon out of it yeah it's
changed completely in that
thirty five year period and
since even the beginning of
the um you know beginning
of the uh twenty tens since
I mean I think we market
them at two thousand eleven
fifty percent of our
operational energy is gone
manufacturing is coming out
of it so it's decarbonizing
rapidly one of the most
important things is it's a local material
It comes from down the road.
When we did our study for
where these materials come from,
they come from less than
forty miles from you.
It'll be a local supplier
that you know that you see
traveling up and down the road to you.
That helps us an enormous
amount with sort of
sustainability benefits.
I understand it's a common conception,
but we sat there with one
of the heads of the biggest
house builders,
volume house builders at
the Future Homes Conference
a couple of weeks ago and
said something not dissimilar.
But a lot of this is
measured over a short period of time.
It's measured over a six year period.
And we are getting a very
different picture with
modern methods of measuring.
some of the some of what we
call the life cycle tools
coming out very very
positive about the whole
life aspect of what happens
with these buildings but we
then expect these buildings
to last even longer you
know it's the same as the
car kind of thing you know
you buy a car and it gives
you the three-year figures
for the car but you don't
buy a car expecting it you
don't buy a house expecting
it to last sixty years you
don't expect to knock it
down and then start again
at that point so all the
things we talk about
sustainability and I
understand that's a common conception
It's not necessarily a correct conception.
There's a lot of aspects
behind that which change.
And we have a full plan to decarbonize.
It's literally part of what
we do on a day-to-day basis.
We talk decarbonisation day
after day and we have
published route maps.
The Low Carbon Concrete
Working Group have got
published route maps.
We, the MPA,
have one specific about
concrete products.
So we know where we're going.
We polled members.
Some of them have declared
decarbonisation by twenty thirty.
Almost every single one has
declared full
decarbonisation by twenty fifty.
We are on that.
journey to remove it and
it's fascinating super
interesting not a
conversation for now but
that's the way I know I'm
very conscious there's a
massive answer behind that
and it includes everybody that uses
wet cast foundations and
block work and everything
that gets involved in this.
It all builds into what that
upfront carbon picture is.
And there's always an
element of concrete in there.
And we're on this amazing
journey to take that carbon out of that.
And I think, Phil,
you've got a right to reply
on that as well, I would imagine,
if you want to.
But before I say that,
make sure you look in the
description of the episode
because all of their
websites are available for
you to click on and find out more.
And I want to make sure you
go and do that and check
out the organisations these
guys are representing.
But yeah, Phil,
do you have... I'm not
actually an expert in this field.
Fine.
But...
at the end of the day, the steel side,
as most, it's in the news all the time,
the amount of effort to go into,
for instance,
in Port Talbot to change the
amount of energy required
to produce steel.
I mean,
I was down there yesterday looking
at what they're trying
We built a building nine
years ago for specific in Swansea,
Swansea Bay with Tata Steel.
We built that.
And over the next three years,
they're looking at taking
it down and putting it up somewhere else.
There's a different building.
Yeah, yeah.
So therefore,
we might not be as
sustainable as some two.
I can take the same panel,
move it to somewhere else, or share it.
It just has to stay within
that design of that eight
foot by four foot panel.
It's going to go there.
And that's what we made.
And I'm not sure whether Richard,
do you need to have a reply
to that comment or is it being covered?
A lot of that's been covered
on the commercial concrete side.
In terms of polystyrene,
it's a natural byproduct of
the oil refining process.
And when used as insulation,
once the building is operational,
it will offset its own
carbon footprint three
times over at least every
year for the rest of the
lifetime of that building.
As we were saying,
these long lifetime structures.
um that's a lot of offset so
it's an understandable
comment but there's a lot
more to it than to be able
to just make a blank yeah
for sure on the on the
timber frame which
obviously isn't it isn't a
solid timber structure as
as robs what you can see
behind me is the insulation
is not a natural material
it's a material it's a
product called pir which is
um oil-based product
but our customers sometimes
want to use a natural
insulation such as hemp or wood fibre,
sheep's wool, that sort of thing.
The reason why that one
there behind me is so
popular is the bang for
your buck that you get with it.
It's very good performance
for the thickness that you get.
so usually if you've got to
go for a natural product
sometimes you've got to go
a bit deeper which means
the timber frame panel's
got to get deeper and it
can be an additional cost
but um with timber frame
you can go fully natural in
terms of insulation as well
okay well I guess you don't
even need to have a reply
to that because you're like
going he's shouting for you
yeah exactly I mean you
know we're using all
natural products so even
the insulation we actually
use a wood fiber insulation
as standard yeah so
everything that we're using
is natural and obviously
The tree grows,
it's finding carbon as
we're cutting trees down.
The forested area in Finland
is growing year on year.
So more trees are being planted,
more carbon is being banned.
So we don't even have to
think about carbon
offsetting because we're
taking more carbon out of
the environment than we're putting in it,
even with the processing.
So we know from studies and
evidence that's been
carried out that it takes
about fifty percent less
energy to process wood than
it does to make cement-based products,
eighty percent less energy
than it does to make bricks.
So processing wood in itself
is a very sustainable and
environmentally friendly system.
Now I'm getting tense.
I can feel the tension.
So I'm going to quickly
because I'm conscious.
I need you guys to answer
this quickly because of the timing.
I only got as far.
We didn't get to you with
the cost side of things.
Yes.
Again, with the market we're in,
the designs can be massively different.
It will depend on the design.
And we've got a cost
calculator on our website
that gives out generic
figures for sort of build costs,
just the timber frame part
and the total build costs.
As a rough idea,
just for the structure of
the timber frame,
we work on about a three
hundred pound per square metre
chart cost for that but that
doesn't include the
erecting costs or some of
our customers put it
themselves but you know I
think you can with
everything you look at
about a third a quarter to
a third of the total build
costs being the timber
frame costs is a good
benchmark to work on
Fair enough.
Steve, I think we covered it.
Speak to your local suppliers,
speak to your regional people that,
whether that's through a
builder's merchant or
direct with other
manufacturers you have down the road,
but speak to them.
I mean, it changes around the country,
you know, it's a local product,
so it changes around the
country for where you are.
It also depends what type of
product you're using.
There's everything from
air-creep products to dense
concrete blocks within what we cover.
So they've got variabilities
there depending on energy
performance as well, what
kind of build you're looking
at in terms of masonry is
massively variable.
Advice as always,
which is a really good one,
go speak to your local manufacturer,
pick what type of build method you want,
what product within that group you want.
Speak to your engineer about what fits,
what you're comfortable with,
and then go find what
that's going to cost you locally.
That makes sense.
Robert?
Well, I mean,
we offer a full turnkey service.
So when we're dealing with a customer,
we'll build the house and
we'll start to finish right
down to floor coverings.
We can even do furniture packages.
So what we tend to do is we
work on the client's perceived budget,
their wish list of what they want.
And then when we design the
house and work with them on that,
we've always got their budget in mind.
And so it really is driven
by the client more than the
product in a way, because, you know,
we say it's an average for
a turnkey house,
it's about two and a half
thousand pounds a square meter,
but we don't know at the
outset whether they want a
five thousand pounds
kitchen or a fifty thousand
pounds kitchen,
and obviously that
influences that square meter price.
So for us,
it's more about working with the
client and trying to meet their budget.
What we always say to everybody,
and it'll be the same with
all the systems,
is if the client has a
sensible budget that you
can build a three-bedroom
house or a four-bedroom house,
whatever it is they're looking for,
all of these systems would suit.
We can change things within
our system and within the
specification to meet the
budget that they're looking for,
but it just needs to be realistic.
No, I understand that.
There's a whole load of
other areas that I would
love to be able to cover,
but I'm being shouted at because I can't.
But what I want to just make
sure is that the website
addresses for all of these
gents are in the episode description,
as I said.
So make sure that you grab
that and you can have a
look and find out more.
Get in touch with you guys
as well to find out.
How many of you were here at
the show at the end of the month?
Make sure you get yourself signed up.
Again, it's on the screen.
The sign up is completely
free to go as long as you
book in advance.
Loads of parking here, as we always say.
We are actually going to be
previewing that show a
little bit more when we do
the episode seven, which is on Tuesday,
the twenty first of January.
I think we're going live at
about one o'clock for that one.
um and we will preview that
in more detail the show and
uh and as you hear these
guys are going to be here
as are many others for you
to find out this is what I
love about doing these
episodes there are so many
things to find out so many
experts to feel uh speak to
and this is the beauty of
this place they're all
under one roof that we
can come and speak to you
heck I even bring them
together and create a fight
you know that's absolutely
fine so you've got the
website there you're able
to uh to get yourself
booked on all sorts of uh
talks that will be on as
well we'll be previewing
that as I say in episode
seven but from gents thank
you so much for joining me
I'm sure you're the same as
me thinking I still want to
talk about more
I suggest everybody comes
and has those conversations
but thank you for to you
all thank you to everybody
watching thank you for the
uh the comments sarah
appreciate that thank you
so much very informative
I'm glad you think that way
uh sarah come and find out
more and we'll see you on
the the next episode in uh
in a couple of weeks time
so I'm just going through
to what I need to do see
you next time cheers all
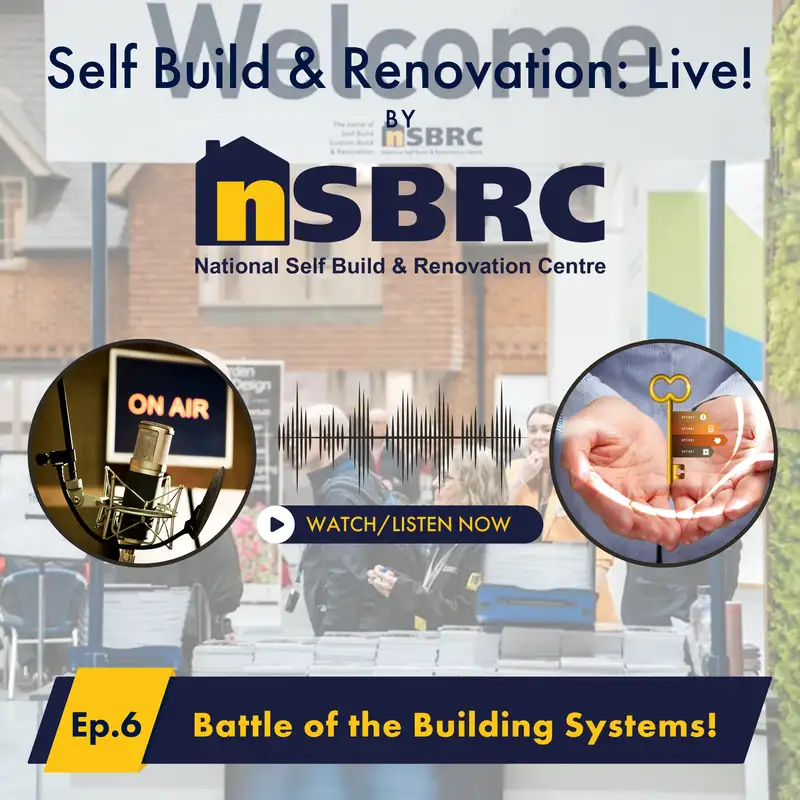